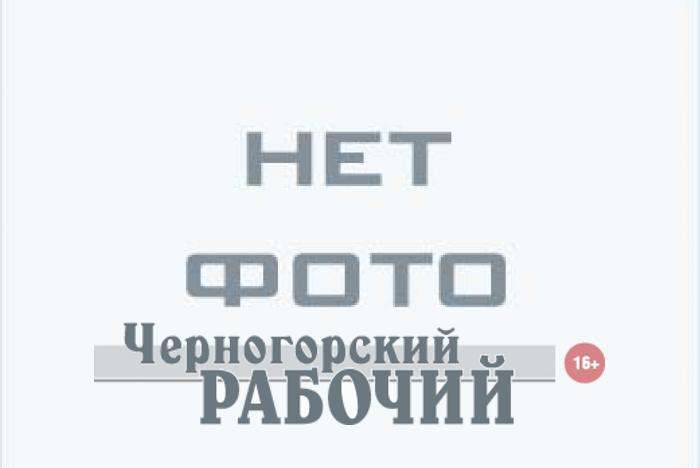
Еще со школьных лет мне нравились книги в жанре «производственного романа». Интересно было читать о различных производствах, о работе агрономов и сталеваров, инженеров и строителей. Чем-то заманчивым и загадочным веяло со страниц, когда автор рассказывал о простых буднях предприятий. Но это для него, автора, все было просто и понятно, читателю же не всегда и далеко не сразу раскрывались тайны.
Помню, как в книге «Кануны» Федора Белова наткнулась на описание работы литейного цеха: «по-самоварному мирно гудела посреди цеха жаркая вагранка да порой вверху, на завалочной площадке, гремел шихтой завалочный ковш. С первой утренней сменой должны были разлить чугун. Шиловский разогнул затекшую поясницу и пошел за опокой. Бригада только что ушла по домам, а ему оставалось заформовать последний стержень». За таинственными словами «вагранка», «шихта», «опоки» стояло чудо рождения новой детали. И все же не все было понятно, ну как, как в ящике с землей появляется пустота нужной формы, в которую заливают металл?
Секрет раскрыли рабочие литейного цеха Черногорского ремонтно-механического завода. Не раз прежде доводилось слышать высокую оценку деятельности этого подразделения, и вот, наконец-то, удалось своими глазами увидеть процесс.
Рассказывал о тайнах литья мастер цеха Сергей Будяк, специалист, влюбленный в свое дело. Недаром же сменил он профессию шахтера на рабочего литейки. А ведь проработал на шахте «Хакасская» ни много ни мало, а одиннадцать лет. Но душой всегда тянулся на РМЗ. Как говорит Сергей Евгеньевич, с производством на заводе он был знаком с детства, там работал его дедушка, не в литейном цехе, но водил мальчишку на экскурсию туда. Тогда-то и появилось желание самому стать к ковшу с расплавленным металлом. Начинал в цехе слесарем, затем стал формовщиком, заливщиком, с годами вырос до мастера.
- Каждому, кто впервые попадает в литейный цех, сразу становится интересно, - говорит Сергей Евгеньевич, - и раскаленный металл, который льется из ковша, как водичка, и формовка, куда он заливается. Я когда в первый раз сюда пришел, стоял и смотрел на металл, не мог оторваться, настолько завораживающее зрелище! Студенты, приходя на экскурсию, тоже стоят, раскрыв рты.
Первое, что встречает в литейном цехе – электродуговая печь. Именно сюда рабочие укладывают металлолом, а на выходе получают огненный металл. Одна загрузка составляет порядка 1,2 тонны лома. Привозят его с разрезов, шахты, других предприятий. Таком образом в литейном цехе не только изготавливают нужные заказчикам детали, но и дают вторую, а то и третью жизнь отслужившему металлу.
Печь в цехе немолодая, разменяла уже третий десяток, но по-прежнему справляется с ответственной задачей – дать плавку к сроку. Тем более что не так давно ей заменили медные шины – этакие толстые кабели из скрученных медных жил, по которым подается напряжение, и надо сказать, немалое – представьте, только для одной плавки требуется порядка полутора тысяч киловатт!
Чтобы расплавленная субстанция не прожгла корпус, печь сложена из специального жаростойкого кирпича, внутренняя поверхность покрыта футеровкой из жидкого стекла и кварцевого песка, благодаря этому остывший металл достаточно легко счищается со стен. Выдерживать печи приходится немало, ведь только для выплавки стали температуру необходимо довести до 1650 градусов по Цельсию.
- Работа у нас коллективная, только все вместе можем обеспечить положительный результат, - рассказывает Сергей Будяк. – У нас нет строго разделения по специальностям, на разливе работают сразу пять человек, каждому есть дело – один крутит штурвал, чтоб наклонить ковш, другой управляет балкой, третий следит за тем, чтобы расплавленный металл заливался в форму.
Черногорская литейка дает плавки чугуна, бронзы и стали. Много лет скрупулезная работа проводилась «на глазок», хоть и опытные специалисты трудятся в цехе, но не всегда удавалось сразу угадать нужное соотношение ингредиентов для той или иной марки стали. Порой то кремния было мало, то, напротив, марганца переложили, в итоге приходилось начинать плавку по-новому.
Но в прошлом году проблема перестала быть актуальной. По инвестиционной программе СУЭК в цех приобрели спектрометр, обучили лаборантов, и теперь точность каждой плавки как в аптеке. Заложили в печь лом, расплавили, специалист провел анализ и уточнил, чего и сколько надо добавить – из контейнеров тут же достается необходимое количество ферросплавов, в основном марганца и кремния, добавляется в «котел», еще раз кипячение, и все: плавка готова. К слову сказать, могут в литейке готовить и редкие сплавы, для этого запасены никель, молибден, титан.
- Сегодня наш цех единственный в Хакасии, так что спрос большой, - продолжает Сергей Евгеньевич. – Обращаются с заказами как угольные предприятия, так и сторонние заказчики. Поточное производство нам не конкурент, не всегда человек может получить ту деталь, которая нужна с большого завода, мы же сделаем. Бывает, дают очень тяжелые и габаритные детали, например, весом в тонну, но ничего, справляемся.
Помимо того что черногорские литейщики могут изготовить даже редкие детали, они еще и помогают экономить заказчикам. Дело в том, что сегодня многие предприятия перешли на новую, высокопроизводительную импортную технику. Уже никого не удивишь «Либхерами» и «Комацу». Да вот проблема, запчасти к ним влетают владельцам в копеечку, а куда деваться – без деталей машина работать не будет. Вот тут-то на помощь и пришли мастера литейки, научились у себя в цехе отливать различные ножи и коронки. Сейчас как раз ведется работа над коронками для «Либхера». А теперь представьте экономическую выгоду: на импортном заводе одна коронка стоит порядка 32 тысяч рублей, а РМЗ ее изготовит всего за 14 тысяч!
Безусловно, процесс отливки будущей детали крайне увлекателен, с одной стороны, несколько пугает река раскаленного металла, а с другой – завораживает. Кажется, требуются особое умение и смелость не бояться плавки, ведь температура о-го-го! Но мастера уверяют, что к этому быстро привыкаешь, главное - не забыться, не потерять уважения к металлу, внимательность и точность - залог успеха.
Но прежде чем приступить к литью, необходимо подготовить формы. Вот тут-то и таился вопрос – как им удается создать в специальной смеси, внешне похожей на простую землю, пустоту? Тайну раскрыл опытный формовщик с 35-летним стажем Михаил Семенович Лаптев.
Итак, в специальную формовочную смесь, которую ограничивает металлический ящик без дна – опока, мастер вбивает деревянную модель будущей детали, причем модель состоит из двух частей: верхней и нижней. После того, как модель вбита, в ящик опускаются стоймя две формы – одна готовит отверстие для заливки металла, другая - для прибыльной части. При остывании металл дает усадку, и чтобы изделие было без раковин, устанавливается прибыль.
После поверхность посыпается сухим песочком и начинается укладка третьего слоя этого специфического пирога. Точными движениями Михаил Семенович вбивает облицовочную формовочную смесь вровень с бортиками опоки. На первый взгляд кажется, что ничего сложного тут нет, вспоминай детство да играй в куличики. Но на самом-то деле работа формовщика требует большого опыта и аккуратности. Ведь после того как смесь будет утрамбована, наступает самый ответственный этап: мастер поднимает верхнюю часть опоки вместе с половинкой модели. Здесь самое главное - точность и расчет. Необходимо очень осторожно извлечь обе половинки модели из смеси и вернуть верхнюю часть опоки назад. Вот так-то и образуется в глухом ящике то самое пустое пространство, куда после плавки будут заливать металл.
- Когда деталь остынет, мы отбойным молотком проводим грубую обработку, а затем отправляем ее в цех, где на механических станках станочники доводят ее до готового вида, - объясняет Сергей Будняк. – Ну а дальше она отправляется к заказчику. Как видите, вроде бы ничего особо сложного в нашем цехе и нет, но согласитесь, интересно. А для нас важно то, что изделия пользуются большим спросом, значит, мы выпускаем качественную продукцию.
Из помещения мы с Сергеем Евгеньевичем выходим на свежий воздух, тут же к нам подходит мужчина:
- Ну как там с моим заказом, успеете? – спрашивает он мастера цеха.
- Конечно! – отвечает Сергей Будняк.
Валентина СОСНОВСКАЯ, «ЧР» №49 от 30 апреля 2013 г.