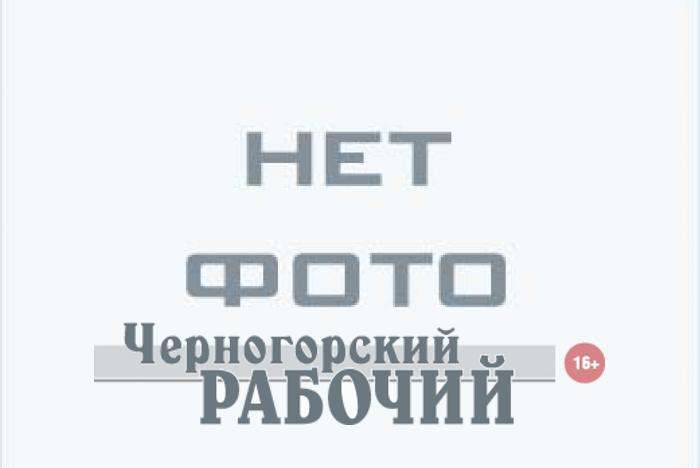
Лето в самом разгаре, и на новом корпусе обогатительной фабрики работы идут полным ходом – не за горами сдача в эксплуатацию.
Издалека кажется, что модуль уже полностью готов к работе, не видно привычных стрел кранов, синяя обшивка ярко выделяется в лучах июльского солнца. Но стоит зайти внутрь помещения, прислушаться к царящим звукам, и понимаешь – стройка еще идет. Пока вместо гула обогатительных машин слышны шипящие звуки сварочных аппаратов, перестук инструментов.
Идея реконструировать фабрику появилась четыре года назад. Специалисты «СибНИИуглеобогащения» провели исследование качественных характеристик перерабатываемых углей, сделали анализ и предложили руководству компании ОАО «СУЭК» концепцию обогащения угля. После чего заключили договор на разработку технического проекта реконструкции фабрики с увеличением производственной мощности до 6 млн тонн в год.
- Реконструкция была насущно необходима для фабрики, - говорит начальник отдела по переработке товарной продукции ООО «СУЭК-Хакасия» Виктор Рыжов, - сейчас у нас не обогащается уголь класса ДСШ 0-13мм, иначе говоря, отсев. Качественные характеристики отсева невысокие: зольность 22 процента, калорийность порядка 4700 Гкал. На рынке этот уголь мало востребован, и на складах год от года его скапливалось большое количество.
И впрямь, значительная часть территории вокруг фабрики окружена терриконами угольного отсева. Юркий погрузчик шустро перемещает горную массу, но черные холмы так и не уменьшаются в размерах. Между тем, специалисты говорят, что после обогащения зольность мелкофракционного угля снизится до 12-14 процентов, зато калорийность вырастет до 5200-5400 Гкал. А это уже уголь, соответствующий экспортным требованиям. Да и отечественный потребитель желает покупать первосортное топливо. К тому же СУЭК изначально делала ставку именно на качество отгружаемой продукции.
- Технология строительства данной обогатительной фабрики не уникальна, но с другой стороны, не существует типового проекта, каждая фабрика строится по индивидуальному проекту, с учетом особенностей технологии переработки углей конкретного месторождения, - поясняет руководитель проекта строительства Николай Антошин. - По проекту фабрика рассчитана на обогащение шести миллионов тонн угля в год, но уже сегодня заложены определенные конструктивные решения, которые помогут перерабатывать больший объем.
На фабрике будет вестись обогащение в тяжелых средах, такой же метод используется и на старом модуле. Однако есть и нововведения. Это применение тяжелосредных гидроциклонов, центрифуги, «Decanter», центрифуги «ТЕМА». Особое внимание уделено условиям труда переработчиков. При проектировании нового корпуса учли недостатки предыдущих проектов, здесь установлена более интенсивная система проветривания, пылеподавления и аспирации. В приточных камерах смонтировано импортное оборудование.
Когда проект был еще в стадии разработки, то специалисты немало поломали головы – какому способу обогащения отдать предпочтение. Одни говорили, что в тяжелых средах – это вчерашний день, другие утверждали, что способ по-прежнему актуален.
- Наши инженеры ездили в Китай, сравнивали с российскими технологиями, - поясняет Виктор Рыжов. – И выяснилось, что сухое обогащение менее эффективное. В Китае его используют потому, что существуют проблемы с водой, фабрики стоят в безводных районах, у нас же этих проблем нет. Поэтому остановили выбор на мокром обогащении в гидроциклонах.
Но, как уже было сказано, при проектировании учли недостатки старого модуля, в частности, экологический компонент. Дело в том, что по прежней водошламовой схеме, отходы переработки (шламовые воды) шли в специальные отстойники, и качество очистки воды оставляло желать лучшего. В новом же корпусе смонтировали радиальный сгуститель. И по технологии все отходы при обогащении отсева будут поступать сюда. Затем сгущенный продукт отправят под три фильтр-пресса, в результате чего получатся обезвоженная масса и осветленная вода, которая направляется в оборот.
Для того, чтобы обеспечить бесперебойную работу двух модулей фабрики, построено несколько галерей. В частности, галерея 450 предназначена для аварийного сброса отсева. Это сделано для того, чтобы старый корпус фабрики мог работать автономно от нового. Технологическая цепочка такова: первоначально добытый в карьере или на шахте уголь направляется на старый модуль, который обогащает крупные фракции угля. Оставшийся после прохождения грохотов отсев направляется в новый корпус на переработку. А теперь представим, остановился процесс на новом модуле, старому подрешетный продукт девать некуда, и, соответственно, он тоже будет вынужден встать.
Именно для того, чтобы избежать такой ситуации, и запускают 450-ю галерею, она будет подавать отсев на аварийный склад. Таким образом, старый модуль остается в работе, а новый спокойно ремонтируется.
- Будет построена 442 галерея, для транспортировки готовой продукции, - уточняет Николай Антошин. - Пока строительство не ведется, так как это помешает работе старого корпуса, что неизбежно приведет к невыполнению плана переработки угля . А встанет старый модуль на годовой ремонт, отсев уберут и построят галерею. Также для наибольшей производительности и повышения качества угля построим крытый склад готовой продукции. При необходимости, зимой там можно будет «вымораживать» уголь, чтобы убрать излишнюю влажность, и поставлять потребителю топливо высокого качества.
Закладка нового корпуса произошла всего три года назад, и уже близок финал. На сегодня выполнено порядка 95 процентов строительно-монтажных работ, смонтировано технологическое оборудование, полным ходом идут набор и обучение рабочих.